When the ground shook on April 5th, and your home and everything in it started to rumble, it came as a shocking surprise to most. Earthquakes, here? Though New Jersey and many other nearby states had just experienced the strongest earthquake in over 200 years, it thankfully caused little to no damage. As of this week, more than 50 low magnitude aftershocks have been recorded since. Scientists say the ancient faults that lay deep under the northeastern states could cause other low magnitude quakes in the future. Building earthquake-resistant homes hasn’t historically been a priority in the Princeton area, and likely is not a necessity, but wouldn’t it be great to know your house was built in a way to withstand these tremors, so you could have no worries about what might happen going forward?
As luck would have it, there is a local builder who works with a product that can provide some confidence. It’s from ThermaSteel, the leading manufacturer of steel structural insulated panels, which can be used in place of wood to frame a home and make it truly resistant to earthquakes. It is also resistant to fire, pests, hurricanes and is maintenance free – things that are more often a concern in this area. While it has long been used in regions that are more prone to severe hurricanes and earthquakes, being mold and termite resistant, prefabricated and more has made ThermaSteel framing for homes enticing in Princeton as well. Here homeowners are finding these benefits, along with ThermaSteel’s ability to make a house more sustainable, make it a very attractive base for their homes. Such a desire was an important factor when John Cullity bought his home made with this technology.
“My wife is French and I’m Australian. We have a commitment to contemporary architecture with a light touch on the planet. Accordingly, the value proposition of ThermaSteel was a genuine feature for us. Not only did the internal/external finish of the property appeal, but its ecofriendly footprint also gave us a great feeling for the property,” Cullity says.
It was its sustainable attributes, cost and more that led the Calaquian family to choose a builder that uses ThermaSteel as well.
“Lumber was very expensive during COVID, so using a composite product like ThermaSteel was not more expensive. It’s easier to build, like putting together Legos!” explains Pamela Calaquian, who has just moved back into her home with her family after a year of construction reworked the first floor and built a brand-new second floor. “I always wanted my house to be more sustainable. I even looked into adding smart water recycling, a Tesla roof and hope to add a water catcher for my garden. But once we saw all its benefits, we decided to have Accel Building Company rebuild our home using ThermaSteel.”
The Calaquian’s house felt no rattling during the initial earthquake tremor. Not needing to fear whether the house was structurally intact was an added benefit they hadn’t planned for! What they did plan for, better sustainability, is something one hears often around Princeton. Homes that tend to deplete fewer natural resources tend to not only be better for the environment (high on many people’s priorities), but also better in the long run for one’s pocketbook. Ideally, they help to make your life easier, all around. That is what led Michael Rotenberg, owner of Accel Building Company, to try out ThermaSteel in the first place.
“My first project was my own home that I built in 2007, in Fair Lawn, NJ. I hate maintenance of any kind. That’s why I spent about a year researching construction materials. My goal was to find a product that would be cost effective and minimize maintenance long term,” shares Rotenberg. “We lived there for 10 years. Our average PSE&G bill was under $300 per month for a 4,600 square foot (sf) house with 11-foot ceilings. I am always on the lookout for new technologies. As of today, there is nothing on the market that comes even close to ThermaSteel panels by any measure. Usually, any material has cons and pros. There are no cons in the ThermaSteel building system.”
Stick-build, which is the traditional house-building method, first uses wood for framing, then installs sheathing, a vapor barrier and insulation. Whereas ThermaSteel panels are a four-in-one composite made to perform structural framing, insulation, sheathing and provide a vapor barrier all-in-one. The panels are made of a continues mass and not of brittle material. That means they will not crack and crumble like normal masonry. Accel Building has had a long-standing relationship promoting and using ThermaSteel for the last decade.
“It takes 100 trees to build a 1,500-sf home while our system only requires steel from 2 recycled cars. I love Princeton for many reasons. One of them is the town’s commitment to keeping Princeton green. For example, if I need to cut a healthy tree to make space for a house, I am required to plant new trees elsewhere on the property. By building a 3,500-sf home out of ThermaSteel panels, 300 trees are saved to start with,” Rotenberg exclaims.
Wood, used to frame most homes, expands and contracts with the weather. Unlike when screwed into ThermaSteel panels, screws and nails into wood can pop and cracks can develop that are not structurally dangerous but can be eyesores and cause design complications. Home settling, as this is referred to, creates a situation where perhaps the alignment isn’t perfect, or furniture must be placed to hide flaws rather than where you wanted it. These are problems designer Giedre Miller says she doesn’t encounter when working with ThermaSteel built homes.
“Another advantage I should mention is that ThermaSteel also allows to pre-design the accurate positions for interior fixtures such as plumbing and electrical systems, cutting out the need for unexpected on-site solutions once the interior framing is put up. Unlike traditional methods where post framing adjustments were commonplace, this eco-friendly material allows for meticulous planning before any material has even touched the site, ensuring a smooth and error free process from beginning to end,” explains Miller, interior designer who works with Accel Building Company. “The two recent projects in Princeton, where I had a chance to work with this framing solution, showcased its effectiveness in streaming the project in its entirety and significantly reduced any pop-up costs, and eliminating any unexpected surprises.”
In addition, the framing of the house takes about half the time piecing together the panels as opposed to stick-build. And, due to the insulation quality of the panels, homes built with ThermaSteel are able to downsize their HVAC systems by up to 50% while seeing decreases in energy bills at the same time.
The Calaquian’s installed a new system upstairs, using a heat pump that is electric, not gas. It pulls heat out of the house during summer months and in the winter, pulls cold air out while pushing heat in. Downstairs they also installed a fireplace with a wood stove insert, which can heat up to 2,000-sf. Today, those elements, the framing panels, in combination with large windows that let in great amounts of sunlight, mean the thermostat has rarely gone above 69° and all feels warm! In March 2024, the PSE&G bill for their 3,683-sf renovated house, with an expanded 2nd floor framed in ThermaSteel, came to $319.88. That, compared $417.16 they paid in March a year ago, when their old house was a little more than half the size, all wood-framed.
“The immediate benefit of a ThermaSteel frame is up to 75% savings in energy costs due to R-Values of up to 61 (which by far exceeds code requirement), and a thermal break between the interior and exterior surfaces of the wall,” Rotenberg notes. “Batt insulation, used in a traditional construction method, loses its insulating qualities over time due to moisture accumulation and crumbling, thus energy costs increase overtime. Since ThermaSteel panels are not susceptible to moisture, energy savings will remain the same for the lifetime of the house.”
Since moving in 2002, the Cullity’s home averages a low $0.04-per-sf in energy bills. John additionally shares that his home is regularly noted to be one of the best performing.
“Based on reports generated by PSE&G our home is routinely rated as amongst the most energy efficient for its size. In plain numbers, energy consumption is broadly 50% of that for homes with comparable square footage,” he adds.
When you’re building a home that’s over 9,500-sf (Accel’s next project!), informing the homeowner they will be benefitting from such energy costs is a huge draw. It’s also enticing that the home is built with zero waste and the steel used in the structure can’t catch fire or create smoke as it is insulated with a component that is fire retardant.
Whether or not other new construction will also look towards more earthquake resistant guidelines following last week’s surprise, it may be too soon to tell. But the owners of this new home will be grateful they don’t have to worry.
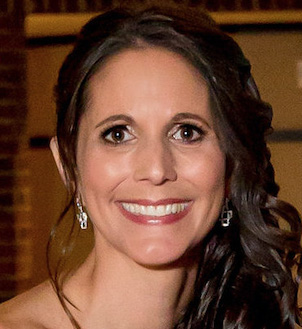
Lisa Jacknow spent years working in national and local news in and around New York City before moving to Princeton. Working as both a TV producer and news reporter, Lisa came to this area to focus on the local news of Mercer County at WZBN-TV. In recent years, she got immersed in the Princeton community by serving leadership roles at local schools in addition to volunteering for other local non-profits. In her free time, Lisa loves to spend time with her family, play tennis, sing and play the piano. A graduate of the S. I. Newhouse School of Public Communications at Syracuse University, Lisa was raised just north of Boston, Massachusetts but has lived in the tri-state area since college. She is excited to be Editor and head writer for Princeton Perspectives!